In early times, laser engraving was the process only useful in industrial companies to either mark parts, tools, trophy shops for customization of awards and recognizing products. Having parts like Amada laser parts and Bystronic laser parts, these machines are known for precise results.
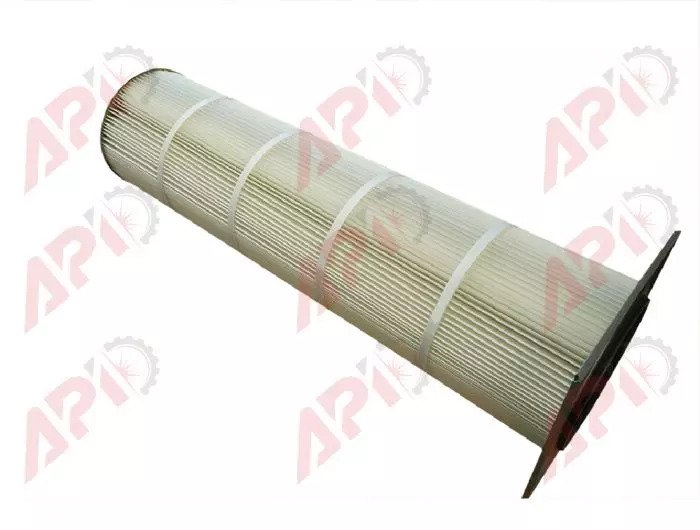
However, today multiple small businesses have started using laser engraving. Today it has grown into a profitable industry and one needs to make an only small investment to be part of it.
According to research by IBIS world, over the past five years, the market of laser engraving has been growing and managing a compound annual growth of 5.5 percent since 2016. The increasing need for customizations and personalization of various products like phone covers, cutlery, wood, metal, or any other materials is driving this industry.
Additionally, businesses are also using these machines for their personal use like customizing promotional materials, in-house signage, employee awards, etc.
With this increase in the use of this industry, its sales are increasing making it easily available and affordable. The continuous growth in this industry is helping small businesses to offer a unique touch to generic products.
Other factors contributing to the rise are a constant increase in personalization, accessibility, maker movement, and branding, new use cases in engraving.
Let's discuss some of the major factors which affect the growth of laser engraving:
- Interest in adding a personal touch:
Have you ever checked out ecommerce website Etsy? You will see the craze of personalization and the way it plays a vital role in the growth of laser engraving. The focus here is to add a personal touch to an item be it a simple t-shirt or things like a pair of champagne flutes and more.
Just a simple search “laser engrave” on Google will provide you with a plethora of personalized products be it jewelry, wedding, glasses, craft suppliers, bags and purses, pen, tools, and many such things.
This recent trend in laser engraving helps small businesses become the first choice for engraving and a way for selling trinkets and other items as well. These things help you to differentiate them from competition.
Laser engraving gives mass-produced items like electronics a personal touch. Engraving custom graphics, names, or logos on gadgets is a great way to set things apart from an ever-increasing crowd of products. Creating such drawings is easier with lasers having Amada laser parts and Bystronic laser parts.
- Easy Access:
Laser engraving machines and cutting systems were heavy and big in old times. Today these engraving machines are not just part of the big factories; in fact, potential buyers can own these machines for far less. If you are looking to own or even rent it then there are multiple ways to do so.
This easy accessibility gave rise to the laser engravers in fabrication labs, maker spaces, school labs, etc. You can even find them will small vendors serving customers looking for customization services.
- Maker Movement:
There are a number ofmakers and they are growing every day as people continue to explore the satisfaction of doing things themselves. DIY has become a new trend and people are learning new skills, creating new things, while saving costs.
Kickstarter and crowdfunding plays a huge role and gives rise to different products that are now available. Some of these products might have not come on the market if not for crowdfunding.
- Rise in Industrial Use:
Other than small businesses, laser engraving is also rising in the industrial segment. One of the biggest segments is in the identification of security where it is a perfect solution for credit cards, ID cards, sensitive documents, and many such things.
Laser engraving helps in permanently marking any item, providing a check and balance against counterfeit products, etc. in ID cards, industries use multilayer formats and are useful to alter the color of low layer pigments without affecting the topmost layer.
This also ensures a product is safe from fraud, produces high-quality images, texts, and many such things. These products are tamper proof and are easily customizable.
Lasers can etch/engrave serial numbers, time stamps, part numbers, component labels, date codes, or any other industry-specific codes. Additionally, it has also become an important part of identification, inventory control and tracking, safety and warning prevention, etc.
With the advancement in technology and parts like Amada laser parts and Bystronic laser parts, the future laser engraving provides an additional security layer that we cannot find in robotics, 3-D printing, and the automotive industry.
Final words:
Laser engraving has a huge scope and market even bigger than we can think. Many of these factors play a vital role in growing the laser engraving industry and today making it a large part of our society.