Being a fabricator can be a difficult job because you need to make sure of hundreds of things like the machining workflow, bending sheets, quality of materials, etc.
While monitoring multiple things you need to ascertain that there is less room for mistakes with productive output.
But, as a fabricator there are many issues you must be facing in your day to day lives be it with the machines, sheet types or anything else.
However, you are not alone! Here in this article, we are going to discuss the 7 most common issues you will encounter and the ways you can solve them with your Press Brake Machine and Amada clamp base assembly, Amada work holders. So, without any further ado; let’s start:
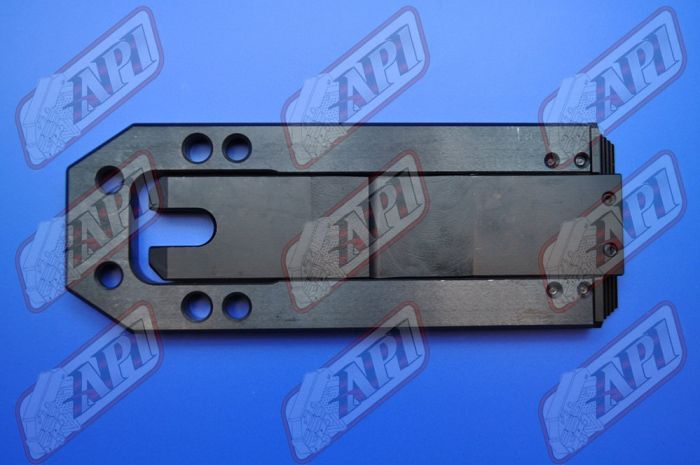
1. Machine not getting started:
There can be multiple reasons for this type of problem like:
- Not releasing the emergency stop button, loose wiring, etc.
- There are also chances of the press brake machine Amada clamp base assembly, Amada work holders not working properly if its main components like thermal relays, overload protection, breakdown of the circuit, damage of AC or there may be some power issues, etc.
Solution:
- Check if the three-phase power is normal, if the wiring has become loose then you can fix it, or if the circuit part isn’t working then you need to analyze the problem behind it.
2. Ram cannot be bent or the bending speed is slow:
Yes, this too can be one of the issues you would be facing. Let’s understand its causes:
- The pressure of things like programming, machines’ tool settings, etc. is not up to the mark, parameters of the Y-axis are not good or the ram is not having a good conversion rate.
Solution:
You need to check the value of the Y-axis. It should be greater than the speed conversion point value. If it is not greater than it, then you will need to adjust the parameters of the Y-axis and also need to make sure that the programming of your operation is working correctly. You need to check if the valves of the machines are proper and are working up to the mark as well.
3. The main motor automatically stops:
There are chances that the main motor may stop abruptly because of overheating, circuit breakdown or any other issue.
Let’s dive a bit deeper into understanding the reasons behind this breakdown:
- Poor oil quality
- If you don’t change the oil in the machine’s Amada clamp base assembly and other parts for a long time.
- If valves are not working properly or the main valve is stuck.
Following are some of the solutions you can use to overcome this problem:
- You need to immediately replace the oil of the machine.
- Clean the main valve and the proportional valve immediately.
- Replace the circuit breaker or can even overheat the switch.
- Make sure to check the system output.
This issue occurs when the backpressure is high and it creates inconsistency on both the sides of the sheet metal.
To resolve this issue, you just need to adjust the backpressure to a specific value and maintain its value consistently.
5. Ram takes too long during transition point:
There can be multiple reasons of this problem. Let’s see each of them in brief:
- Tank suction leakage
- The Y-axis parameters are not good
- There are chances of valve failure during installation or the machine is not getting proper spring tension
Below are the solutions to this problem:
- Start with checking the rubber sheet or re-install the cover of it.
- Adjust the parameters of the Y-axis so your machine is working seamlessly.
- Make sure to check the valve installation is proper, check the spring tension and also check the core of the valve.
6. The calculated pressure is more:
This problem arises when:
- The set of electric resistance is not correct
- The programming of the bending method is wrong
- The machine parameters modify material parameters or unit selection
Solution:
- Make sure that the programming is correct.
- Choose the press brake tooling in regards to plate thickness and V slot width.
- Make sure that you are checking the machine tool parameters.
7. Hydraulic temperature is high:
There are various factors that affect the hydraulic temperature:
- Filter blocking, oil pollution or deterioration, many such factors.
- Working under high pressure for long hours.
Below are some of the solutions you can use:
- Replace the oil and filter if needed.
- Check if there is a reason to work for long hours and high work pressure.
Final Words:
Having issues in the mechanical machine are very common and as a fabricator, you need to understand and try solving them. There might be days when you will face issues that are more critical than this. But, not losing your hope and trying to solve them patiently is the key.
No comments:
Post a Comment